April 23, 2021
Q&A: Laia Mogas-Soldevila, Assistant Professor of Architecture
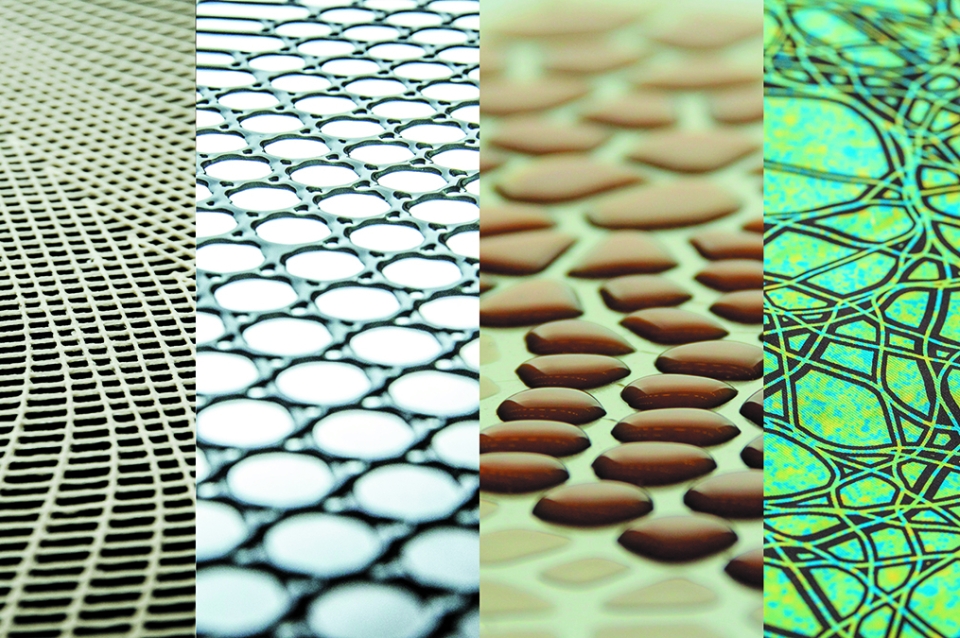
Biomaterials produced with techniques borrowed from the life sciences can be used for everyday objects that biodegrade after use.
Stuart Weitzman School of Design
102 Meyerson Hall
210 South 34th Street
Philadelphia, PA 19104
Biomaterials produced with techniques borrowed from the life sciences can be used for everyday objects that biodegrade after use.
Michael Grant
mrgrant@design.upenn.edu
215.898.2539
Laia Mogas-Soldevila joined the graduate architecture faculty at the Weitzman School of Design last fall, after holding appointments as a visiting professor in Cornell University’s Department of Architecture and an instructor with the MIT Department of Architecture and MIT MediaLab. She earned an interdisciplinary PhD from Tufts University and two master’s degrees from MIT. She co-founded DumoLab, an experimental architecture and engineering research studio, in Barcelona in 2008. DumoLab Research will be her new group at Weitzman in 2022.
This year, Mogas-Soldevila is teaching the seminar New Materials and Methods Research in the MSD-AAD program, and a new elective called Inquiry into Biomaterial Architectures. Because those courses meet online as part of Weitzman’s hybrid approach, she has yet to move to Philadelphia. In her research, she examines the potential for new types of materials to drive the process of design, and the implications for architecture’s relationship to the environment. Mogas-Soldevila was also recently named a faculty fellow at Lauder College House.
Why did you want to come to Penn?
Penn has been on my radar since 2016, when I took part in the Under Pressure: Urban Housing Symposium and had the chance to witness the depth of inquiry here. By 2019, former MIT colleagues were doing great work here, a new state-of-the-art robotics lab was emerging, and I was in regular discussion with senior faculty developing very exciting publications. It felt natural to join the team and contribute to the research vision. After my (virtual) visit and public talk for the community at large, the excitement went both ways, devising new avenues for material-driven research to bridge design and science within the graduate architecture curriculum. I have now taught (from Boston) for almost a semester and met over 50 wonderful Weitzman students. I can’t wait to land on campus in the summer!
Your research is focused on material-driven design. How did you get interested in that and what are the main areas of research you’re exploring?
For the past 10 years at MIT DesComp, MIT MediaLab, and The Silklab at Tufts, I’ve been working on what I call “New Design Companions,” strategies that architects are beginning to use with the aim of reconquering agency in all aspects of the building lifecycle. I started by looking at computational tools developed by designers to escape the rigidity of existing software and devise novel structural geometries. My research soon expanded into practices of incorporating advanced fabrication processes from engineering and allowing for new sets of parameters to be controlled for, and by, design.
In the last few years, I have been increasingly interested in intervening in materials engineering and cross-pollinating new computation and new fabrication with new materials for the emergence of architectural practice that challenges the fragmentation of traditional building construction. I explore material design down to the molecule, what I call “reviving matter.”
My most recent work is reverse engineering biomaterials to form everyday objects with the outstanding properties we find in wood, skin, shell, or bone. My goal is to broaden design research and inquiry starting from the very building blocks of matter and up to the macro scale, responding to the needs for sustainability and efficiency.
How can new types of biomaterials be used in architectural applications? What are the potential climate and environmental implications of material innovations?
A new wave of at-scale biodegradable and environmentally-conscious materials is coming: bricks produced by fungi and agricultural waste without need for firing; micro algae illuminating the city at night without electricity; wood veneer programmed to change shape and control climate within buildings; biopolymers like cellulose, silk, chitin, or keratin, which fully break down after use, replacing plastic parts. For such emerging prototypes to turn into products, a sustainability-first paradigm must govern industry, economy and society. It most certainly will entail replacement of entire modes of industrial manufacturing, reformulation of building code and testing standards, and the integration of biomaterials value and aesthetics in contemporary culture.
In my practice, I embrace both new and old efforts towards ecological integration. On one hand, I find vernacular architecture’s hyper-local material strategies and energy-saving solutions are now more relevant than ever and need to be revised and updated. On the other hand, I look at how biomaterials are used in biomedical engineering and life sciences to develop devices that are digested, implanted, and that heal the human body. Scaling them up to architectural applications is crucial not only to avoid resource depletion, but also to ensure that our building solutions degrade, nourishing the Earth and ultimately ourselves.
What kind of work do you do with DumoLab?
DumoLab is an experimental design studio that my partner Jorge Duro-Royo and I founded back in 2008. Our practice does information-driven design and develops the frameworks for that to happen. We bridge computational design and advanced manufacturing, with projects focusing on structural optimization, multi-scale city data analysis, parametric urbanism, multitouch territorial navigation, industrial robotic interfaces, fabrication information modeling, and we are recently developing advanced interactive data environments.
Your latest publication is called “Additively manufactured leather-like silk protein materials.” What is the story there?
This is an example of the power of designing materials at the molecular level. In collaboration with biomedical and material engineers, we developed soft biomaterial surfaces to replace traditional environmentally-unfriendly animal leathers. Using shrimp shell waste and silk protein from discarded silkworm cocoons, the surfaces were extruded from gels into layers enabling a wide variety of formats. Using a precise set of processes, the resulting materials are not only comparable to animal leathers, but also enable designers to alter their performance in terms of opacity, flexibility, strength or responsiveness. On top of their versatility, their production requires minimal energy and mild chemicals, and their ability to biodegrade facilitates sustainable production.